Ali Khoshmaram, a Senior Process Engineer with Arak Oil Refining Co. asks this question to our LinkedIn Catcracking group. It was a great question that received a lot of equally great responses, so we wanted to share the exchange with our readers here. We have posted the complete exchange below.
What is the best solution for avoiding cyclone blockage in RFCC reactor?
Stagnant regions of cyclones in RFCC reactor have a high potential of coke accumulation and there is a high risk at any thermal shuck (especially cold shutdowns) that this coke falls down and blocks the cyclone dipleg which lead to significant catalyst lost through the main fractionator.
In this case, the consequences would be extremely harmful, 7 to 10 days unit shutdown for maintenance and severe erosion and leakage in downstream equipment like fractionator’s trays, pump impellers and control valves. More than it, fouling in MCB circulation lines and heat exchangers would be observed.
One solution is installing coke anchors around stagnant areas that could hold the coke and decrease the risk. If you have experience of using this feature or have a better solution, please share!
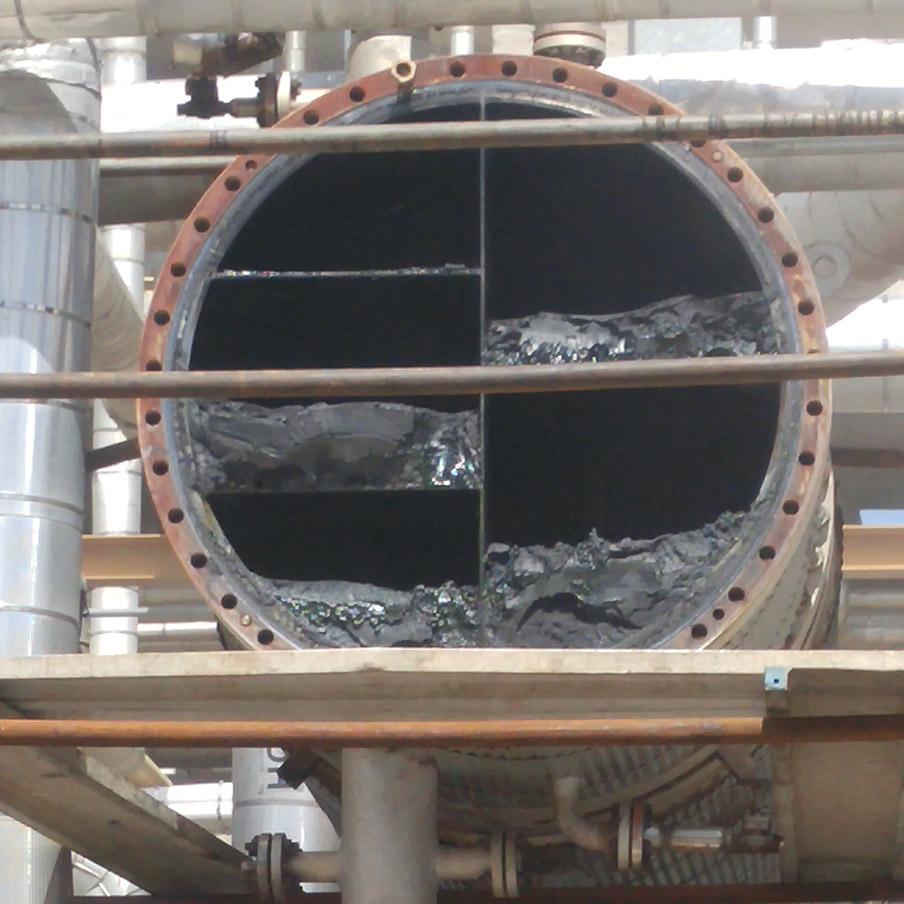
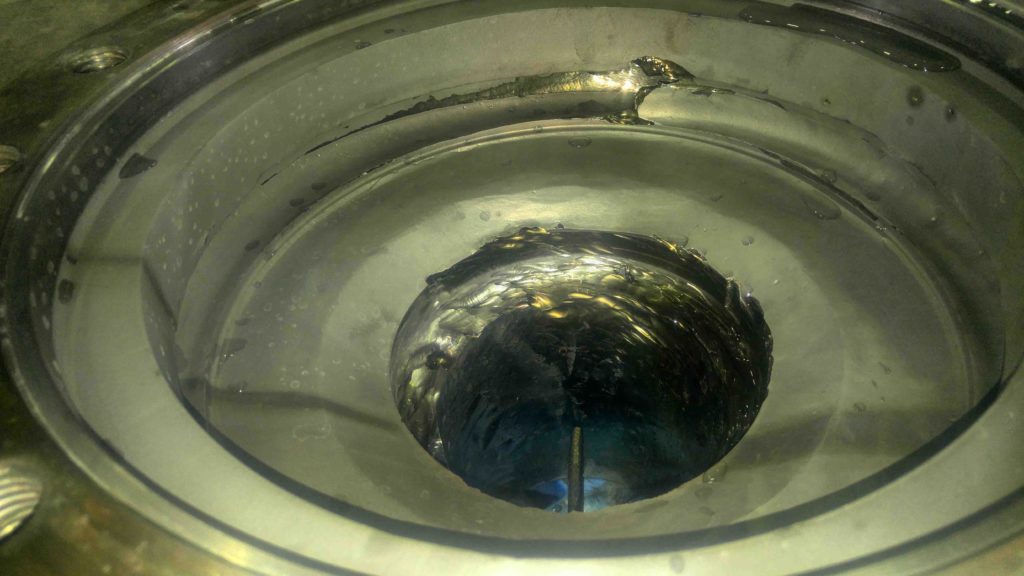
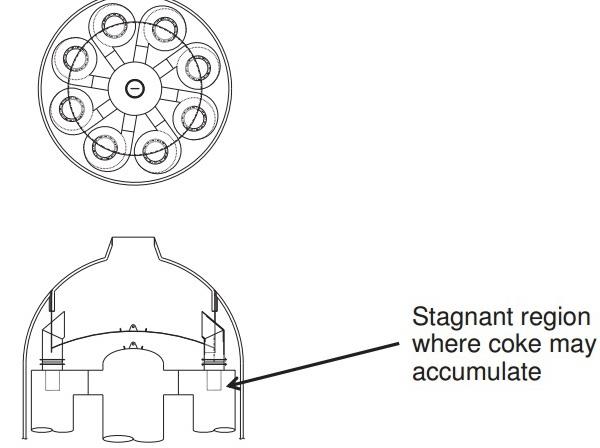
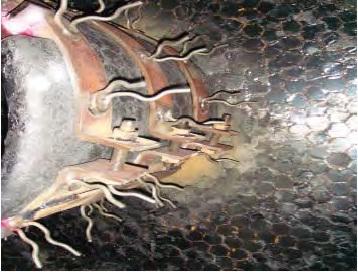
A Process Engineer at Pertamina says:
The coke formation in the downstream reactor is likely promoted also by MCB operating conditions. While in the reactor, it is difficult to avoid but it can be minimized. Large chunks of coke spalled from the reactor section should be retained in the MCB coke trap (you should have this in the unit). Let’s say some small particles pass through, but by operating the section with liquid velocity >1.2 m/s in pipes that will sweep out the settled solids. Try to moderate first your main column bottom operating temp and dilute the bottom liquid with LCO. If you have high coke precursors in the reactor feed, ensure your feed atomisation works well. Reducing the reactor severities, introducing more inert (steam) also help to minimise cokes around reactor.
I would prefer to investigate the root cause of the excessive coke formation either in reactor or main col sections and try to minimize it with the operating condition adjustments before deciding to install something new in the unit.
A Production Team Leader at Hengyuan Refining Company Berhad (formerly known as Shell Refining Company Berhad) says:
Vapour condensation on top reactor could lead to the coke formation. Some units equipped with electric heater can prevent it. Poor or damaged insulation could also be the cause.
A Lead Start-up Engineer says:
It would prevent the coke from falling in the diplegs but not allow the accumulation of it. Sure it is already nice. Do you think a kind of deflector can avoid dead part, to do as a flush of all the cyclone section? (even if it is erosive…).
An Operations Manager at Reliance Industries Limited says:
Stagnant portions shall be filled with moving fluid to have some minimum velocity in the region so that coke is not formed.
A Senior Process and Operation Engineer in the Oil & Gas Downstream Field says:
Very interesting discussion…. Firstly, it is necessary to be sure if your issue is really coke formation in stagnant areas of cyclones. Do you have enough evidence about it? Was any RCA performed? If so, I think coke formation in stagnant areas of cyclone is related to low entry velocities in cyclones… I would suggest making some velocity profiles and checking proper size of crossover, cyclone diameter and gas riser diameter…. I can’t understand clearly cyclones configuration but it looks like you only have one stage of cyclones (only primary cyclones); if so all cyclone entry velocities are related to the feed load, check if you are working at low feed load in this case you can help with more steam or water injection into the riser to increase entry velocity to the cyclones.
Ali Khoshmaram replies:
After opening the reactor we checked all blocked and non blocked cyclones. Only in stagnant areas we found coke accumulation. As UOP recommended the riser velocity should be in the range of 3.5-4.5 m/s. We are working at 85% of design feed but our velocity is in the range. On the other hand increasing steam media in reactor could increase the catalyst deactivation and also make a limitation in main column overhead air coolers.
A Senior Process Engineer (FCCUs & Treating Units) at Astron Energy (Pty) Ltd. says:
I think you need to decide what’s more important. Blocking up your diplegs or maybe losing a little bit of activity. Catalytic activity can be managed by just adjusting the addition rate. I also doubt that if you increased steam rates but stayed within the design limits of the unit, that you’d be able to really discern the deactivation caused by more steam say relative to all the other factors that impact and influence activity. I think if you could find a way to introduce steam into the dead zones, this might be more effective as this would be a more targeted approach… That’s just my view on this. Also as someone pointed out, installing coke anchors will not prevent coke from forming, it will just provide a surface upon which coke will deposit. I think even if you had coke anchors, a time will come when the coke might accumulate to some “critical” mass which might spall off when the unit is thermally cycled so unless you are taking regular pit stops to remove and clean up the coke, I would go beyond just installing coke anchors.
An assistant Block Leader says:
Have you thought about something like an anticoking baffle system?
Ali Khoshmaram replies:
Is such thing applicable in stagnant area that showed in the picture? If so, may you please share more details about it.
An FCC & Refractory Specialist at Inspection & Consulting Services LLC (ICS LLC) says:
Coke anchors on GOP work well and there are many different designs of them.
Another refiner says:
What kind of cyclone system do you have? Our FCCs have direct coupled cyclones with an annular gap located on top of the primary cyclones to allow steam and hydrocarbon vapours to exit the reactor and head to the main fractionator. The annular gap tends to block up after a while and what we have seen is that if the reactors are not decoked every 2 to 3 years we tend to get to a situation where the annular gap is almost completely blocked due to coke deposition. What we did on one of our FCCs back in 2017 was to increase the size of the annular gap when we replaced the reactor cyclones.
Ali Khoshmaram replies:
Maybe try coke anchors as you are already considering this. Alternatively some steam in there might help a little bit or maybe you can do both if feasible from an installation/space and cost point of view.
_______________________
Join our Catcracking Group so you can follow all our FCC-related conversations, share your expertise on this topic, or post questions of your own.
For more information on fluid catalytic cracking, visit Catcracking.com.
Leave a Reply
You must be logged in to post a comment.