Refining investment in alkylation expansions and gasoline octane improvement include production of additional feedstock for the alkylation unit. The primary source of olefin feedstock for the alkylation unit is the FCC unit. Operating conditions in the FCC unit can be adjusted to favor increased propylene and butylene (or butene) production. BASF recently announced the availability of a new FCCU additive designed for butylenes selectivity. According to BASF, its proprietary Evolve FCC additive provides measurable improvements in butylene yields while preserving unit conversion and valuable fuels yields. With alkylate becoming a preferred gasoline blending component ever since Tier 3 standards went into effect in 2017, butylene production has been tight due to gas plant constraints and the performance (or lack of) many of the market’s current olefin additives’ ability to increase selectivity for butylenes over propylene.
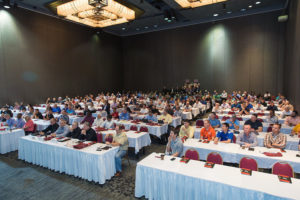
Refiners at RefComm® discuss cooling and chilling challenges with FCC product recovery and gas plant sections.
Regardless, the FCC wet gas compressor becomes the first major bottleneck in recovering incremental production of propylene and butylene. Modifications may be required to the compressor, as well as associated cooling, inter-stage, or after-stage equipment. Aside from the benefits of new catalyst technology such as Evolve, it goes without saying that the need for well designed product recovery systems, downstream from the main fractionator, can be the most capital selective design consideration.
Downstream of the FCC wet gas compressor, absorption or sponging capacity becomes the next bottleneck. According to comments from Burns & McDonald’s Erin Chan, et. al. at the 2017 AFPM Operations & Process Technology Summit, “Increased lean or sponge oil circulation, as well as additional cooling or chilling, can be used to separate the propylene and butylene from the fuel gas stream. Alternately, a cryogenic type of processing unit can be used to cool the fuel gas stream and produce a liquid C3+ product stream.” They also noted that “Downstream of the absorption and sponging columns, the depropanizer and debutanizer columns may be pushed to their limits, with the overhead condensing systems becoming a bottleneck in recovering the liquid propylene and butylene products.”
Besides the increased production of butylene for increasing alkylation unit capacity, comonomer grade butene (1-butene) is used in petrochemical process facilities as feedstock for polyethylene production. For meeting increased market demand, recently developed technology for production of the butene comonomer includes the Lummus Technology Comonomer Production Technology (CPT) from raffinate streams. In the CPT process, 2-butene contained in the butylene feedstock can be isomerized to 1-butene. The butene from isomerization together with the butene contained in the feed is then recovered by fractionation to produce butene product. According to information obtained from Lummus Technology’s website, the CPT process for butene production is based on isomerization technology first developed for the olefins conversion technology (OCT) for propylene production. In the OCT process isomerization and metathesis are combined. In the CPT process, the metathesis catalyst function is removed leaving only the isomerization function for isomerization of 2-butene to 1-butene.
Leave a Reply
You must be logged in to post a comment.